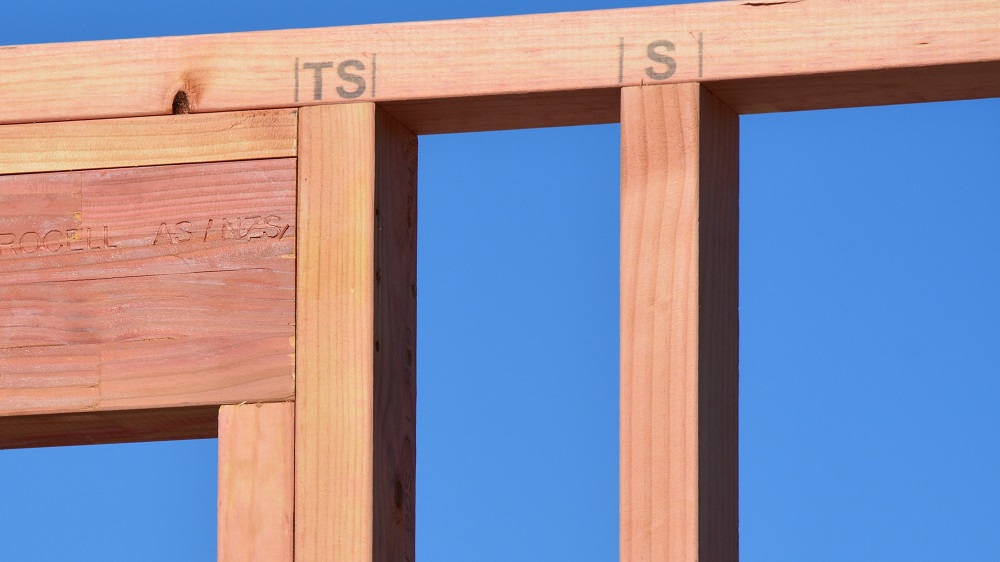
Residential building materials permitted in trusted overseas markets will be automatically approved in New Zealand under a legislative “shake up” of the Building Act.
Building and Construction Minister Chris Penk announced the regulatory reform with Prime Minister Christopher Luxon in Upper Hutt on Thursday morning.
He said the cost of building a home had climbed significantly in the past few years, partly because it was difficult to access alternative building products when supplies ran short.
The approval process for a new material could take up to two years and was blocking competitors from entering the market.
“This red tape entrenches the use of well-known products, which lowers competition, increases the risk of supply chain disruptions like in the recent GIB shortage, and ultimately makes it more expensive to build anything,” Penk said.
The Government will amend the Building Act to recognise product standards used in some overseas jurisdictions and require consent authorities to accept these alternatives.
One example of an overseas certification scheme is Australia’s WaterMark which assures plumbing products are safe and reliable. It alone could add 200,000 products to NZ.
Penk said this was a “major shakeup” that would drive down costs without compromising on standards. The amendments are hoped to be passed before the end of the year.
These changes are partly in response to a Commerce Commission market study into residential building supplies which the previous Government asked for. It recommended making it easier to get building supplies approved in New Zealand and allow for more product substitutions on construction sites.
Penk said the new regulatory scheme may also make it easier for NZ made products to get international approval as they will be benchmarked against approved overseas alternatives.
Some overseas jurisdictions have similar standards but different seismic or climate conditions which may mean some specific products are not suitable in the local market.
115 Comments
About time
I think the product associated with leaky NZ houses originated in Australia...
Plus which, cost of components isn't the problem. Clipping of the ticket, combined with arse-covering, is ti problem.
Not "the" product, perhaps "a" product.
Leaking homes was an industry system failure, from the govt changed building regs, architects, speciifiers, suppliers builders, council inspectors...all designing installing and signing off on products, building systems & installations unfit for purpose.
The point that is forgotten is who told all of those people that the product was fit for purpose? They didn't just come up with the system
Thanks for giving architects the mention ... but here is a perspective often overlooked: less than 5% of residential dwellings in NZ are designed by or have an architect involved in the construction. Notwithstanding that fact, architects cop a lion's share of leaky building press & blame. We can't create and fold a company to skirt liability. On the matter of busting up the oligopoly and cartel behaviour of the well known controllers and manipulators of our marketplace? All for it. This tweak is only a start - fundamental changes in how we build in rhis country is required, and urgently. The construction systems we continue to use and the half-pie ideas about building envelopes that ignore or fail to understand the basic principals of physics and energy transfer are at the root of our inferior buildings. NZ does not need to reinvent the wheel, yet again, and the climate and conditions are not unique here - a ruse that has allowed the monopoly players to hoodwink policy wonks into creating such a beureacratic quagmire so as to discourage entry to our pathetically small marketspace. Simple solutions? No, certainly not. Two things that might get us on a better path? Stop treating houses like investment commodities and break the cycle of doing things on the cheap... so tired of the refrain of 'want' accompanied by the endless refrain of 'we'll beat it by 15%'.
I agree. I have built 2 homes in the last 12 years & our architect (same guy both) was key to achieving a quality result - mainly bec he was experienced & partly bec he listened to & explained carefully to his clients.
He also charged by the hour not a % of the total cost which I understand is rare in the industry, however an obvious driver for professional & customer value.
Bang on.
Time to break down this building surpply cartel.
Cost me $5k the other day for 200sqm of steel for commercail concrete drive what a rip off.
Reposted from my comment a few days ago:
Building cost
I'm currently in Oz & visited a street of show homes in a new subdivision yesterday
This 255m2 - 4brm, 2 bath, 3 living home was advertised house only price AUD256,100.
$1000/m2
https://coralhomes.com.au/house-and-land/highlands-255q-covella-lot-601…
They are really decent houses in that link. The house and land package prices indicate that the land prices are north of $600,000. That is ridiculous and totally artificial given that Australia is so blessed with enormous areas or cheap and useless land. A young person seeing those new home offerings should quickly realize that they are wasting their time in New Zealand. I must sent that link to our kids.
42km from Brisbane CBD which is at best a large satellite city. The land would be worth $100k max? Then there is the rampant youth crime wave in Greater Brisbane (white youth at that for you KK)
https://www.youtube.com/watch?v=nI4JTpCKv78
$940k to live in suburbia miles from anything - coming to a city near you thanks to National.
If it were so cheap to build houses in Aus there wouldn’t be a severe rental shortage in Brisbane.
We asked & were told that the house could be built on our own section for that price (within a certain km distance from authorised building agents), we saw the advertising sign on the Gold Coast.
Land prices typically double build cost
Ohhhh...Fletchers protection blanket just has a hole torn in it.
I'm really surprised (and impressed), they did it. Nice!
Fletchers must not have have upped their National Party donations to the same amount as the roading and landlord lobbies.
Here we go again! Follow the saga of Fletchers and the Chinese copper pipes they installed in Wellington's regional hospital. Or how about the toxic Gib we had coming in a few years ago? NZ suppliers have had it too good for too long, but blanket moves like this are just plain dumb!
Sounds like you have experience here, what would you do to qualify these new products without making compliance too expensive or delay their entrance to the market unreasonably? Genuine question.
Good question and I'm not sure whether there is an easy answer. Having some decent homegrown standards and regular testing of materials governed by other standards used to be the answer, but wasn't a lot of this was dismantled in the 80's/90's?
Another is enforcing accountability when things go wrong - including at importer and licensor level - and at Government level if practices it enables result in an inferior built environment. Not the duck for cover rubbish we saw with monoclad.
Indeed. Give BRANZ back some clout as the logical choice to interface and monitor materials & systems from the 'approved' jurisdiction authorities might be a start. Remove building from the behomouth MBIE too. Finally, actually fund the important and relevent work undertaken by BRANZ and especially remove the commercial viability aspect imposed back in the 1990s - forcing reliance on advertising, sponsorship and financial contributions from industry players casts a taint on the impartiality, at least in perception...
Stiff penalties for bad conduct and no ability to hide behind shell companies.
If you knowingly bring in a shitty product then you should feel the consequences.
Just make sure you don't know...
Stiff penalties? Like guzzling champaigne on your yacht in the Med, after you've wound your "company" up?
Looks like aiming to place greater responsibility and accountability in the common ground of the contract between builder/constructor and buyer/owner. That in turn puts the onus on either party to properly cover themselves by way of that contract being adequately detailed, rather than thinking to fall back on local and/or central government regulations. For instance builders may require to provide personal guarantees behind their operative company and they may need similar guarantees themselves from suppliers of materials. Experience of late in our family of a new build over a several faults the builder blamed the supplier’s product and the supplier blamed the builder’s work.
Sounds like you have experience here, what would you do to qualify these new products without making compliance too expensive or delay their entrance to the market unreasonably? Genuine question.
Just remove any guarantee or warranty.
Granted I'm only talking about exterior products, but unless they're tested over a long period of time in NZ, there's no way to ensure something from overseas is fit for purpose.
Drive out to Muriwai, to the north of the golf course are fields of products being tested in our environment. And other places around NZ. If you don't do that, you will be testing them in the market instead.
Often the problem is not the product itself but how the product is used in conjunction with other products and what building regulations say is acceptable in NZ.
A good example of this is kiln dried timber. It's used successfully all over the world. BUT ... the rest of the world has different building regulations that have more stringent rules in moisture protection & removal. (Or they don't need the more stringent rules because the location never has a problem because they get far less rain, and wind driven rain.) Thus a like-for-like use of kiln-dried timber to replace treated timber in NZ with our building regulations was a disaster waiting to happen.
One issue with the kiln dry in NZ is much of it is laminated offcuts. Even though the manufacturers will claim it's all Tickety boo, the joins in the laminates are always a potential point of failure.
Australian - Crane enfield metals not China. Also looks like a proper filter which was present elsewhere where no copper pipe issues occured wouldve prevented the issue.
Lets not throw the baby out with the bath water yet.
Are they talking about letting in cheap rubbish from any low grade country or products from first world countries that meet recognized international standards like ISO, JIS, BS, ASA, NIST, ICC .........? Looking at the disasters that our building code has allowed, I think that I would prefer products that conform with these other standards. I strongly suspect that our own building standards are developed by a group of not overly bright NZ building industry interests who are more strongly motivated in developing standards that make it difficult to import competing products.
Having said that can someone explain how overseas the external walls of houses can be constructed with what looks like strand board with not a lot more than building paper to keep the moisture out? Am I missing something? Is there something special about the strand board and or the protective membrane?
Risky? Havent we tried this experiment before, nz home-buyers are the guinea pigs
From what countries, as there are different standards, also different climates
Perhaps read the article
"One example of an overseas certification scheme is Australia’s WaterMark which assures plumbing products are safe and reliable. It alone could add 200,000 products to NZ."
Here's an example of a WaterMark certificate of conformity. Note the Brand Name in the Product Schedule.
https://www.iplex.com.au/assets/Uploads/542dac1159/Iplex-Profit-Fitting…
Building and Energy has carried out testing on pipe samples taken from affected properties. Findings so far show the leaks are principally from Pro-fit pipes manufactured by Iplex Australia between mid-2017 to mid-2022
https://www.commerce.wa.gov.au/announcements/update-pipe-leaks-new-homes
From another article:
The party proposed allowing any material or system approved for use in the American, European, British, and Australian markets to be automatically approved in New Zealand
https://www.interest.co.nz/property/127121/zoning-housing-regulations-a…
Californian weather tightness systems (where it almost never rains) allowed in Auckland (where it rains every day in winter)?
English bracing systems allowed in ChCh?
It sounds like a good idea in theory until you dig a bit deeper...
No one’s importing Californian weather tightness systems. Any imported product will still need to be installed to our standards.
Cheap steel reo and non uv stabilised plastics ect are more where things might turn to custard.
You can install something to our standard, but if the materials aren't good that's irrelevant.
You install it to the manufacturers standard, the building code doesn't mandate how to install anything other than the very basics.
"Acceptable solutions"
If a product or system is given acceptable solution status then yes installed to manufacturers standards. If it’s not then to use it you need to prove it meets the building code. As far as I know that’s not an easy process. It’s a very different code to what it was 30 years ago.
Never rains in California? Dont take geography lessons from song lyrics. Northern California (San Francisco, Sacramento etc) get plenty of rain.
https://www.sfchronicle.com/projects/weather/california-rain-totals/
And each city has different building regulations.
Jimbo's point stands. You can't just take products & systems from any place they have been certified. Each place is different.
But it doesn't rain in LA, I used to live there. Maybe some around Christmas time. That's where convertible cars originated, because it hardly ever rains.
Even in NZ, we get architects based in cities, designing town houses for erection in what are close to rainforests.
They might be to code, but they're not to purpose.
Bit different if we're talking mass scale subdivision housing though.
...architects? or perhaps you mean architectural designer, or architectural draughts... or any of the myriad of names and descriptors that imply architect but don't specifically call a person an architect. When they are not. Because clearly that is against the law... and clearly the informed NZ consumer understands the difference. 🤣😂 Sorry Tui, but Yeah, Right.
Some of these people are registered architects. If not an architect, I don't know what to call them.
Even yourself, call yourself an architect, and say there's nothing specifically unique about NZ - there's a reason we've one of the highest skin cancer rates in the world.
Architects definitely have their place and for me its in house design greater than $750k, that's the house only not including land. Architectural designers and draughtsman have their place and provided they are LBP registered are suitable for run of the mill houses at a lower value. I've always had the perception that architects are good for doing pretty when most of the design, even for a residential house is related to structural engineering. Case in point. I'm looking at a small project, value wise, where the design is 90% structural and SED, 10% doing pretty. I'd have the structural engineer as principal with an architectural designer do the layout. Fortunately I have an engineering background and house design is a hobby. Average Joe Blogs would not see it this way.
more new products into the market is a good thing. though it doesn't mean more sellers in the market. unless we have more stores in the market, the existing stores will just maintain their profits margin.
What it the point of cheaper houses when being robbed blind by local councils who cant stop giving money away to useless causes.
Kapiti is talking about a 17% increase, while the government sits back on its thumbs
You need to think wider - which will put you ahead of many....
Councils, like health, universities, and central governments, are in trouble. They presumed endless growth - and in that, they were factually mistaken. We are up against the global limits now, and as the quality of the remaining resource/energy decreases, rates, taxes and costs must rise - until the system implodes.
My oft-told example is that it once took the removal of ten tons of 'overburden', to get at one ton of copper (think: plumbing). That was done with 100:1 EROEI oil. Now we're down to 400 tons removed, to get at a ton - and the EROEI is down to 15:1, probably less. Don't blame the Councils - that's just small-thinking 'otherising'.
I'm not sure that this will make much difference. Framing timber, wood cladding, concrete, roofing iron no change. The high cost of labour and contractor margins will not change.
Will this go down as another National party disaster.
Leaky homes Bolger/ Shipley government.
Heavy trucks destroying our roads Key government.
A brand new disaster Luxon government.
She'll be right mate
"high cost of labour" - yeah, I never understood why a builder per hour in NZ costs 3x what a builder in the US does.
If only those US carpenters knew of this earning differential we'd never have a builder shortage.
It's because we are not connected to Mexico
In California, you can get illegal labour really cheap. But if you're working on something that needs certifying, you have to use legit workers. Those cost more than legit workers in NZ.
Housing costs in NZ are very high, it translates into what it costs to do business as people need to charge enough to pay their rent/mortgage.
The only real answer is more competition across the entire building process including land.
You need to look at the exchange rate for one, the cost of living and the the cost of tools. Can buy a good brand bench saw over there for $300 on special. Same saw here is $1500 including gst on special last month
Perhaps you are another one of those people that believe carpenters should be living in cardboard boxes for the privilege of building you a mansion
Good. The protection racket has gone on too long.
Hallelujah!
Does NZ currently build the best houses in the world? If not, then opening the market to overseas products from where they do build the best houses can only improve standards.
Nowhere builds the best house in the world, because the world's a diverse place.
The Scandanavians make wonderful timber products, but many of them fail here.
The brits use a lot of brick, its great if you don't have earthquakes.
It seems a lot of the comments are letting perfect be the enemy of good.
This is way better than what we currently have and long overdue. Haters gonna hate?
I agree, it's great news. However I still think an element of caution is needed before we open the flood gates to allow any product with a Standards Mark approval to be used.
Local Councils adopt an inhouse product approvals list in 3 waters, why not the Government for building materials? It usually includes "Manufacturer" and "Supplier/Distributor" for which there's an established, reputable supplier in New Zealand that can front liability. Otherwise you risk unscrupulous businessmen flying into the country with a briefcase of Standards Mark certs to arrange drop shipping of their manufacturer's reject products.
It will be the councils that get smashed, National seem to have a vendetta. They won't be allowed to prevent a material that is certified overseas, then they will get the bill when it fails and the builder and supplier have fled.
Its a good idea if there are just a few issues a year, but if an entire decade's housing stock gets affected its a really bad idea. I also have my doubts that it will save that much anyway.
Remember "leaky houses"?
That too was the National Party deciding they knew better about how to build houses.
Surely if people buy from a reputable builder with a watertight third party quality guarantee. Then the issue of ensuring quality lies with the builder/guatantor to select and competently install products as needed...or they won't be able to offer guarentees again... where they choose to source materials from shouldnt be a concern for the buyer who will be covered..
If there is an issue with the third party guarentees then we should look there.... ideally it would all be market driven with government control on the stability and adwquate funds over the guarantor?
You can get guarantees, but often these preclude lack of maintenance.
Much of the leakers were relying on silicon or other perishable membranes for water tightness. Which work fine on the day of completion, but in 10 years, if not maintained, your weather tightness is disappearing.
A great initiative. Just make sure you have the product knowledge to recognise quality among the cheap and nasty.
You may have missed this 'recognise product standards used in some overseas jurisdictions' and they gave an example of Australian Watermark.
This will only work for the low cost and volume builders.
Any builder that is willing to stand behind his product, hasn't got 10s of thousands in a fund to defend themselves and doesn't want loose their own house will just refuse to use imported products that have no testing or comprehensive warranty.
Gee kiwi are naive.
The building supply industry has been a cartel for ever in this country there is margin on margin on margin.
Been in the game for years its a joke.
Hopefully this will help.
Remember the word Cartel there is a lot of them running in this country.
This needs to stop to get the country back on track
Yes they've been clipping the ticket big time. Add all the council fees and the health and safety sharks. Nothing but a rort.
They are not saying 'no testing,' they are saying products that have the equivalent or greater testing than the NZ standard (which isn't that hard to meet) will be allowed.
In most cases there is no comparable NZ standard. Cladding for example, the standard is that it must survive NZ conditions for a minimum of 15 years, how does an overseas product adhere to that? Even Gib, it’s used for bracing in NZ and has been tested to meet the strength requirements, but foreign Gib is not used for bracing or tested for it.
Any overseas product can currently be consented if it proves it’s up to those standards, but that’s expensive to do.
Keep drinking the GIB coolade - of course a dfferent colour paper face and sometimes a mesh in the mix of your 9.5/10/12&13 mm gypsum composition panel, with the array of different prices for said 'differences' is superior to all the other gypsum based wallboard products everywhere else in the world. Look how they saved Christchurch buildings... oh. That's right. Of course our local special conditions and superior marketing - oops I mean manufacturing - is unrivaled and that is why Knauf* realised there was no chance to gain marketshare from the superior player well established and dominating here. At least until the unexpected hiccup with production...
No modern building in Christchurch that relied on gib board to brace it collapsed, so I'm not sure you know what you're talking about. Gib has only been used as bracing since the 90's as the testing was only brought in by the 1991 Act.
PS gypsom based wallboards are not used so predominantly as bracing in other countries because, gosh, somehow those countries have figured out such products aren't actually so great to be relied upon for seismic resistence. Or maybe our manufacturer has cornered the international supply of magic coloured papers that mitigate seismic forces.
No, there is no requirement for them to actually test here in NZ, only that the NZ authorities like BRANZ or other product certifiers confirm that it meets NZ requirements, which they can easily do if the imported products have used certain overseas testing authorities.
In many cases, the NZ testing standard is a watered-down version of the overseas standard, but with legislation and a near monopoly on who you can use NZ, then it has stopped many great products from being imported.
As one overseas supplier of Passive quality materials told me, they had never seen a first-world country with such poor building standards and yet certification costs that were the most expensive of any of the 40 countries they export to.
Good enough for Aus, good enough for NZ. How about we apply it to professional qualifications well.
If it is just Australian standards then it is probably fine, but the devil is in the detail and we don't have that yet.
New Zealand houses have minimum lifespan requirements of just 50 years for the building's structure and 15 years for the durability of the exterior cladding.
Who exactly were we protecting from imported competing building products?
Well last time deregulation went wrong it cost the country between $11 and $23 billion to remedy depending on who you ask. As a ratepayer and taxpayer I helped pay for it, but most of the cost fell on the building owners it seems: https://en.wikipedia.org/wiki/Leaky_homes_crisis#:~:text=Overview%20Gro….
Most of the leaky home failures were from using the wrong design for the limited range of materials available and in some cases poor installation.
In short, it was a lack of understanding of basic building science and still is for many designers and builders.
The 15 year durability requirement for cladding is an excellent limitation. We recently tore off all the old hardiplank on our house that was installed circa 1991, and replaced with new lineaboard. Would have preferred to go with weatherboard, but schedule 1 building act requires like for like without needing consent. If we sell, and it had weatherboard without consent, would have been an issue.
However, I note that Auckland Council is acting ultra vires in requiring ALL recladding (even where it is more than 15 years old and has not leaked) to be consented, even where new cladding is like for like.
I asked AC for the legal provision on which they are overriding Schedule 1, but nobody was able to give that information.
would be good for an enterprising journalist to investigate and ask if AC are illegally charging for reclad consents in those situations.
Encouraging people to reclad with like products is fundamentally stupid. If it worked properly then chances are you wouldn’t be recladding it.
AC are truely a bunch of muppets.
AC don’t make the rules, MBIE do. It’s the same rules throughout the country, must be like for like or needs consent.
If you read the previous comments you would see that apparently its not the same rules everywhere as AC is requiring consent for like replacement
Correct. AC are the only ones doing so which is in contravention of the Building Act. AC consent requirement does not trump Schedule 1 of the Building Act.
It’s not the only way Auckland Council make their own rules.
(Deleted comment after more research)
I'm not sure if that's completely correct. You can replace steel tiles with longrun, both classified as light roof. In older houses , around mid seventies there was no roof underlay under the tiles. Replacing with longrun requires roof underlay and you need an LBP roofer to do the install, but no building consent.
Hardiplank certainly doesn’t look the best after 30 years. It also wasn’t the best for keeping paint adhered to the surface in its later years. Nothing wrong with replacing it with the much more durable, and advanced, lineaboard that can be painted satisfactorily. We did this outside of Auckland, but if it was in Auckland, AC would have (illegally) asked us to obtain consent which the Building Act explicitly states is not required for a reclad of like for like exterior which has satisfied the 15 year durability requirement.
You can paint almost anything if you prime it properly first.
Linea isn't without it's issues, although that's mainly appearance (the manufacturing creates a textured finish, which is often less consistent with visible blooms).
AC can’t ask anything, they either take you to court (which they would lose if you are correct), or they don’t. If it does not need consent, it’s the same rule throughout the country.
Apply for a determination from MIBE. Still costs but cheaper than getting a consent. They don't set a precedent, but if enough of them get filed they might pull their heads in
Schedule 1 of the Building Act does limit the application of the 'like for like' provision:
"However, subclauses (1) and (2) do not include the following building work:
(a) complete or substantial replacement of a specified system; or
(b) complete or substantial replacement of a building product or an assembly contributing to the building’s structural behaviour or fire-safety properties; or
(c) repair or replacement (other than maintenance) of a building product or an assembly incorporated in or associated with a building that has failed to satisfy the provisions of the building code for durability, for example, through a failure to comply with the external moisture requirements of the building code; or
(d) sanitary plumbing or drainlaying under the Plumbers, Gasfitters, and Drainlayers Act 2006."
So Auckland Council sees a complete recladding as covered by clause (a), and thus needs a building consent.
People seem to be conflating more choices and more supply of individual items with somehow that will result in better design, better assembly of the individual items as a system, and better installation of said items and systems.
I suspect councils will counter this by asking for complete systems verification eg full wall assemblies tested as one unit.
After all, leaky homes and the Grenfell Tower all used approved individual items that failed as a complete system.
This move by the Govt. is good news, but is just one small step on the many that are needed.
Leaky buildings from 1980,s. No eves,flat roofs,internal gutters,Our house originally built 1950s,on piles approx 1 metre off ground,framing is untreated, recent renovations,framing all good.
It will be NZ native timber framing not pine.
My parents house build in the 60's. Rimu joists and tawa flooring.
Haven't we seen all this before?
Remember the leaking house crisis? New houses will never be cheaper to build. There's entrenched costs that are very unlikely to decline, like local body gouging. More inspections, more drains, more tanks etc.
Fantastic. About time. For too long, too few a companies have had the NZ public by the short-and-curlies on building products. Next step will be ensuring those responsible for specifying a product in a build have future accountability for their decisions.
And the other problem of course, is, do you want your house built by a genuine kiwi builder or an asian immigrant?
Asian builders don’t knock off at lunchtime Friday and go to the pub,and they work weekends.
I know right? I’m mean, WTFs wrong with them?
Trouble is most don't speak any english.
Surely they can just point to the tap for a beer.
So another one that wants indentured slaves rather than craftsmen
Depends which builder will spend every moment they can talking to you about how they're going to make a killing in Riverhead.
Riverhead's a good place to start if you want to make some serious moolah.
But I'm now well aware no one here is interested in having some fun and getting rich. They'd sooner talk about how hard life is.
And how we need some socialist intervention.
Doesn't really matter the nationality of the builder. If they're managed and overseen professionally, not really a problem.
Big "If" though. Project management in 2024 has little to do with building knowledge.
most Nz electrical, plumbing and gas standards are based on international standards anyway.
Yeah, so a lot, let’s say 90% of the standards, is just wasted.
Our standards need to be by exception.
In electrical, they kind of act as a summary , saves having to look up several iec standards or whatever.
The difference in cost between say Marley conduit, and imported product stamped with the nz standard is huge. I don't know what hoops they had to jump through to be able to bring the imported stuff in, wether it had to be tested here, or just cross referencing standards.
Well, new materials aren't necessarily the problem
They need to fit a few fundamental requirements including:
1) Must be fit for purpose, and exceed any design life requirements - which are surprisingly short in NZ
2) Must be safe to use and install and dispose of at end of life (i.e. non toxic - not asbestos)
3) Be cost effective and increase competitiveness in the industry
The real issue is around design principals, 'weather tightness' is a stupid concept - as these typically rely on correctly installed flashing or sealants which deteriorate over time. I have seen too many industrial buildings that are 50+yrs old with internal gutters and not one of them has not had leaky gutters or water damage issues
Most external cladding systems are 'weather/ water deflection systems' which is why internal gutters are such a stupid idea and ultimately lead to failure... either through sealants failing or drains blocking and having nowhere to go but inside the building causing massive damage and repair costs
Likewise keeping water away from your foundation is important too, and often overlooked which can lead to differential settlement - uneven floors/ cracks in walls/ doors jamming etc
There are reason that 100yr old homes lasted so long, they had good ventilation, deflected water outside of the building envelope, never had internal gutters and were made from quality timber, insulation/ electrical/ pile foundations were rubbish in hindsight and led to issues later but the bones and core design principals were robust, excluding insulation, wiring, plumbing and other systems which were just poor at the time
We need design principals in play which can mitigate product failures, such as we implemented post leaky home with having to have a cavity between cladding and frames so even if water got past the first cladding barrier then there is a physical gap and a second weather barrier (wrap) to protect the frames - and having airflow between them dries out any water so they do not rot the frame
Unfortunately what looks good/ sharp and what's practical are not always on the same end of the design principal spectrum
We welcome your comments below. If you are not already registered, please register to comment.
Remember we welcome robust, respectful and insightful debate. We don't welcome abusive or defamatory comments and will de-register those repeatedly making such comments. Our current comment policy is here.